Mold접기
Mold is used to manufacture cores and POSCO MOBILITY SOLUTION applies its international recognized proprietary technology in die manufacturing. The company holds a number of patents for the mold technology. Its proprietary engineering and manufacturing allowed the company recognized in the market.
POSCO MOBILITY SOLUTION started to manufacture the tooling for EI lamination core in the beginning of 1980 and developed the high speed tooling for motor lamination core through the stacking technology. We also design and produce the highly precise toolings autonomously by tooling R & D center established in 1989.
We supply various types of toolings & controller system for self-developed multi-cavities motor lamination core, double cavities rotation stacking tooling of thin plate, motor lamination core tooling for HEV.
We are consistently striving to enhance the efficiencies and characteristics of the core by studying plasticity, flexibility for the electrical steel.
Type & Application
We promise the best possible quality and maximum productivity in the motor manufacturing industry by applying the multi-column motor core mold and the 0.2T motor core index double-column mold, which were developed by POSCO MOBILITY SOLUTION, and the Index Skew mold and Controller system using the Servo Motor.
-
- Motor core mold for eco-friendly automobiles
- A mold which has developed the auto lamination technology with large sheet materials in line on a leading basis, by which improving productivity and yield rate and eventually maximizing customers’ value.
-
- Multi-column AC motor core mold
- A mold to realize multi-column system for mass production, in which the mold achieves stable volume due to the distributed weight on each stage and the super-precise 3- or 4-column manufacture technology.
-
- Rotational laminated mold
- A mold to rotate each sheet in order to reduce the materials’ thickness deviation but improve concentricity of products, which requires the level of precise location as well as highly precise manufacture/maintenance technologies.
-
- Transversely movable die mold
- A mold to move upper and lower punch and die in a transverse direction where each sheet of core gets blanked with consistent change in product surface, on a super-precise control basis.
Mold Technology Research Institute
It is a place where excellent professionals are conducting research. The Mold Technology Research Institute packages self-developed stacked molds, controller systems, automatic stacking systems, etc. so that customers can conveniently use them to meet their needs. It ensures the best possible quality and productivity.
-
Counter Bore
If it is structured in one or two layers to install bearings in the rotor shaft of the motor, it is possible to stack them by controlling the count per layer.
-
Skewing
If each slot has a slope to minimize the noise or abnormal vibration of the motor, we can take any angle to the motor core in the mold.
-
Indexing
To reduce the deviation of the thickness of the steel plate, it is possible to improve the quality of products by rotating at various angles for stacking and minimizing the deviation of thickness, and choose either the motor type or the mechanical type as the drive mode.
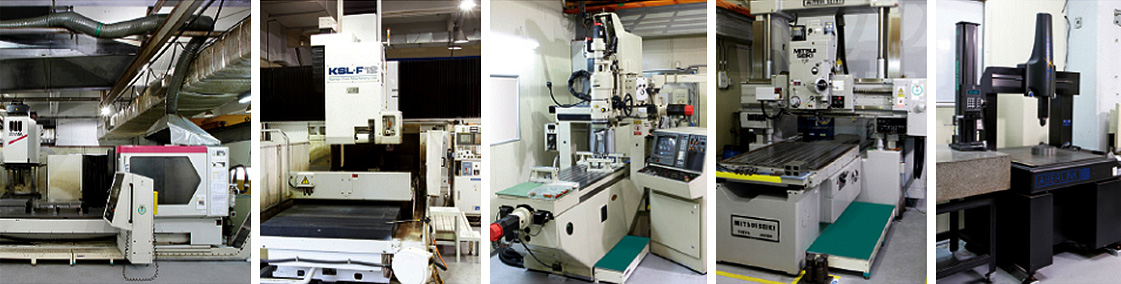